So now that we know more about the BMW/Getrag Dual Clutch Transmission from chapters one and two, we can further learn how to control all the spinning gears and clutch packs. Currently, the best way to do that is with the HTG GCU (Gearbox Control Unit). The GCU is a transmission controller that works in a very similar manner to many of the standalone ECU’s on the market. It is as configurable as you can imagine and has no OEM software or safeguards to work-around.
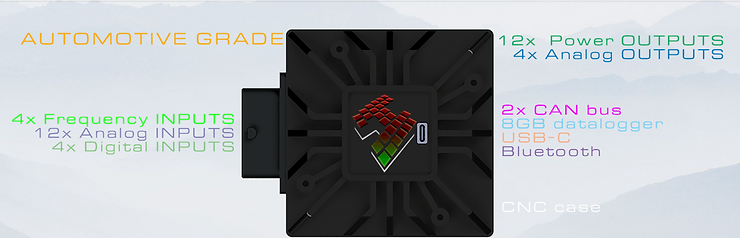
HTG is a young and growing electronics company out of Poland that is not only committed to supporting the continued development of the DCT transmission (and many others) in aftermarket applications, but also offer the highest quality hardware we have come across. HTG also has the most developed tuning/configuration software by a large margin, which is constantly being updated so that transmission control is more streamlined with each update. More staff is being acquired to continue to offer the growing community support, a growing instructions database and most importantly; quickly responds to any questions you may have about the GCU and its implementation via email, live chat or their very active HTG Tuning Community Facebook group.
After testing several solutions, and the factors previously discussed, we have become an authorized dealer for their products as we believe it is the best solution on the market for use in both crazy and mildly upgraded OEM vehicles. We stock them in the USA and support customer needs with our knowledge, relationship with HTG, and our accessories which make implementation as simple as possible. We believe HTG to be the leader when it comes to transmission control.
The most intimidating task of integrating the GCU into the vehicle is the transmission wiring. The project requires soldering wires to small transmissions sensor pads, making sure trigger wires don’t interfere with signal wires, and making sure enough power can reach each solenoid (This is measured with HTG valve test software before installation to be sure). The wiring of the GCU requires the removal of the original onboard computer housed inside the mechatronics module. The mechatronics is the removable module that houses this “computer”, the sensors, and the solenoid valve connections. The computer board is bonded to the mechatronics case and can be removed with a chisel. This is not necessary, but looks nice. The tiny wires going from the sensor pads to the mechatronics are how the original computer gets al of its information. Once we remove these, we can solder our own wires to these pads to essentially hardwire the transmission ad bypass all OEM control. If you would like a wiring kit, or us to wire your GCU, please email us or purchase on our online store.

For HTG wiring instructions please follow the link: https://drive.google.com/file/d/1-UBSHbpfbaOFbWAaHtKeT-1huKsw2zNs/view?usp=sharing
For wire recommendations using our DCT plug please see link: https://docs.google.com/spreadsheets/d/1j2G6Sq48GfBc-24l_wXGSaT-VBJaOxC1LHvSH3omXrQ/edit?usp=sharing
Shifter Wiring Information: https://drive.google.com/file/d/1H1wGWBFqAsagrX579KgnFiYiFBtRiWj6/view
Wiring Tips and Information
Power In: Two 12v power wires, paired with two chassis grounds, give the GCU the juice it needs to function. Make sure the grounds go to a solid chassis ground. Constant 12v wires require a 30 amp fuse and should be switched on and off via a relay. If they are to constant battery power they will drain the battery. A single ignition switched power wire (Pin L1) is what triggers the GCU to turn on and off. Always fuse this wire with a 5 amp fuse. We run this on the same circuit as the ECU power.
Power Out: The GCU supports 12 main outputs. These can be configured to either be high or low side, meaning they can send 12 volts or switch to ground to activate. When configured for the BMW DCT 10 of the 12 wires are used to ground trigger the transmissions solenoid valves. The extra two outputs can be configured for other things like triggering a relay for a reverse light, cooling fan and more.
For all of the sensors, triggers and accessories the GCU has both a 5v and 12v power supply. These should never be used to power anything but a sensor or trigger, but it is plenty capable of providing all the sensors the power they need to work correctly. The same goes for the Sensor Ground: Never use it for anything but providing the sensors and digital inputs a stable ground source, and never pair it with the chassis ground wires.
CAN X2: With two CAN channels the GCU can be configured to get all the vehicle data while using virtually no standard input wires. This can greatly reduce the amount of wiring needed. The CAN channels can be setup to “speak” with the engine controller such as any popular standalone, factory ECU, or dashboard for all the information it needs to function (RPM, TPS, etc).
A channel can also be used to communicate with an OEM shifter which is quite a nice touch in a road car with a full interior. CAN channels have configurable BUS speeds and have no built in terminating resistors so you will need to add them to the wiring if you are only communicating with one other module on the CAN BUS. 120 ohm resistors should be on either end of the twisted pair BUS wires.
Analog Inputs: Unlike its competitors, the HTG GCU uses all of the analog sensors in the transmission to make the most educated shift decisions possible. These include the factory DCT temperature sensor you can tap into to use for driver information or a cooling fan relay system. 8 of the 12 analog inputs in the GCU are used by the DCT sensors and the 4 remaining can be used to provide the GCU ancillary vehicle information if it is not available via CAN. Common examples of inputs like these would be pedal/throttle position, clutch pedal position and manifold pressure used for GCU torque calculations in boosted applications.
Digital Inputs: Unlike analog inputs, digital inputs are either on or off. These are useful for things like paddle shifters. If you want a set of really nice paddles, check out ours for sale,
All digital outputs care ground switched, meaning to engage, they must complete a cricuit to sensor ground.
Analog Outputs: Similar to analog inputs, these outputs provide outside devices information in the form of 0-5v or 0-12v signals if they can’t be communicated via CAN, This can be configured to do things like provide gear position, transmission temp, gear cut, and throttle blip requests.
One of the most interesting and entertaining aspects of the GCU is the ability to use a “virtual clutch”. Using an analog input you can clutch override and engage, slip, and lock the clutch like a normal hydraulic clutch pedal. The most popular way to integrate this is with a electronic throttle pedal in the clutches position, but rigging up any 0-5v input will work. Even a button can be set up if all you like would be an on/off clutch kick. This virtual clutch feature is very useful for launches on variable surfaces, drifting (clutch kicks), and for loading onto the trailer.
Minimum Inputs: If you are installing the DCT into a vehicle using a simple setup, the minimal amount of inputs the GCU needs to function are engine RPM and TPS/PPS (Pedal Position is always better than Throttle Position). The later is a simple 0-5v analog input, while the RPM can come in over the Frequency 4 input (square wave). We will have signal converters for RPM in our store which are often helpful for this (Even works for cars with a distributor!).
Valve Testing: When wiring to the solenoid valves one must take care to use wire that is thick enough to supply the power needed to all solenoids. Since the 12v solenoid supply is shared among all the valves, care must be taken to wire so that there are no interference issues when firing the solenoids. Please see our wiring chart here for recommended wire gauges. We like to run two 14 gauge wires to the mechatronics, and then split them out into 16 gauge fingers to each valve. Then, we run 18 gauge (quality TXL wire) back to the GCU for low side ground triggers. Once this is complete the valve test software is extremely useful for validation. The goal is to see each valve trigger, and not have any other valve raise itself more than 10% of the triggered valve. You will always see some variation, but a consistent pattern is the goal. If wires are too thin some will rise up which can cause issues later down the road once the transmission is in the car. Please see picture below of a successful valve test.
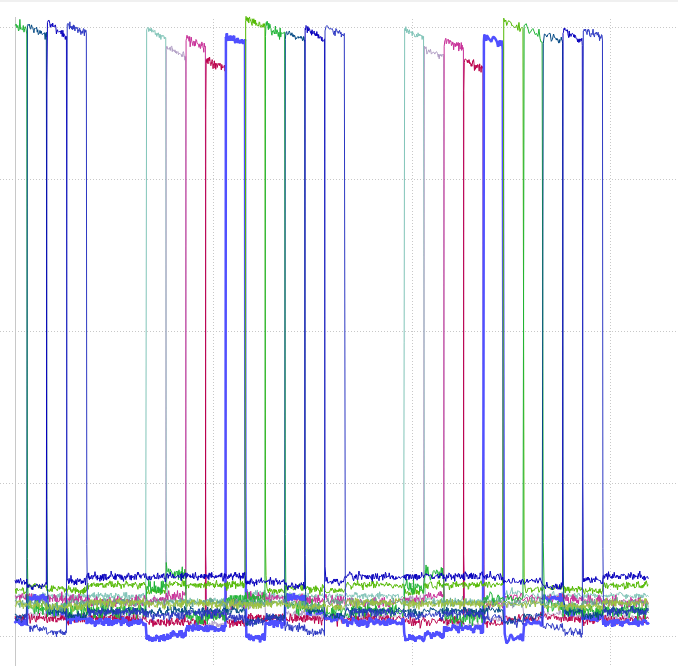
Shift Selector Options: One has a few options when setting up shifting. Using the OEM BMW Shift selector is very nice and wired via CAN. This is a very clean way to integrate the DCT into any road car. If you have another selector you would like to use, HTG is very open to setting up the software/CAN to accommodate.


Another way is to use paddles. These can be wired separately to digital inputs, or via one wire with resistors to an analog input. In a racecar application this is the most simple way, but you can also add buttons for reverse, neutral, drive etc. Or, you can rely on configurable shift logic such as hold downshift for reverse. Another popular option is to use the DCT shifter. This is an extremely stiff shifter (not something shared with a video game) that really feels like shifting a sequential transmission. This can be wired the same as the paddles.
Our favorite way to wire the shifters is also the most simple since it is used in a race car. We wire upshift and downshift to sensor ground, along with a neutral button. These are each configured as digital inputs in the HTG software. Changing gears and using reverse is as easy as pulling the paddles. Nothing more.
Note: For gear cut settings, one must set up the ECU to hold gear cut as long as the signal for, the GCU is active. The GCU will hold this signal until all needed conditions are met. For this reasons, set gear cut time is not recommended.
Thanks for reading, if you have any questions feel free to email us!
Leave a Reply